
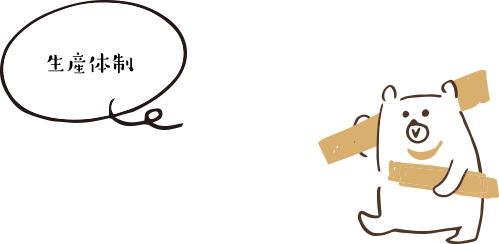
弊社では、生産を自社工場で行うという利点から、利便性・対応の早さを活かし、生産への安心と信頼をお客さまへご提供します。 厳重な検針体制を特徴とする工場の生産の流れもご覧ください。
工場での生産の流れ
生地発注から納品までの、ぬいぐるみ生産の流れを細かくご紹介します。
生地発注、入庫後の生地検査
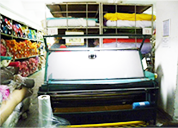
生地入庫後、写真の機械を使用して、色ムラ等の不良が無いか生地のロール検査を行います。
生地の裁断
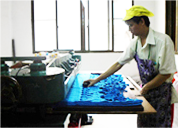
裁断型を作成後に生地の裁断に入ります。随時、裁断型・裁断品の変形がないかチェックを行います。

毛足が長い生地は裁断機を使用すると、毛並みが崩れてしまうので、生地の裏側から熱裁断を行います。
刺繍
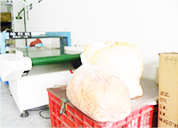
裁断後に刺繍を施します。刺繍が施されたパーツは検針作業を行います。(検針1回目)
縫製ライン
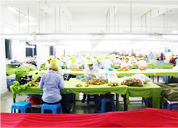
生産見本をもとに縫製を行います。
危険物管理ボックス。刃物の紛失や混入を未然に防ぐために、休憩時には、必ず一人一人が名前入りの専用ボックスへはさみや針を保管する事が徹底されています。
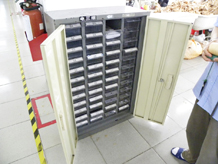
縫製後の検針
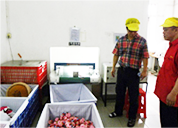
全ての縫製終了後、綿を詰める前に検針作業を行います。(検針2回目)
1時間に1回、検針機が問題なく作動するか、写真のボックスを使用して、上中下左右合わせて9カ所の針反応の確認を行います。

綿詰め作業
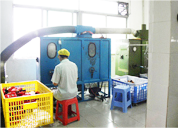
決められたグラム数に合わせて、機械で綿を詰めます。細かい箇所は手作業で丁寧に詰めていきます。
綿詰め後の検針
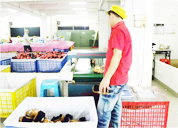
綿詰め作業後、すぐに検針作業を行います。(検針3回目)
仕上げ・形状チェック
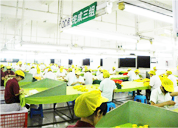
生産見本をもとに、糸色・縫い数・形状の確認をし、ほつれ等の外観検査を行います。
梱包ルームへ
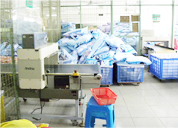
仕上がった商品を目視でチェック後に梱包前の検針作業を行います。ここではL字型に配置した検針機で、商品の縦方向1回、横方向で1回の計2回検針作業を行います。(検針4回目)
梱包ルームへ入る前には、エアークリーンで身体のチリやホコリを取り除きます。
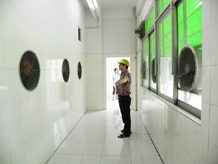
パッケージ作業
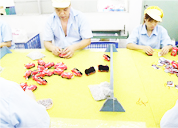
紙タグや袋詰めの作業を行います。
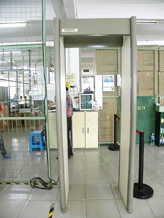
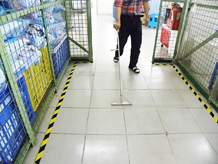
パッケージ作業ルームに入る前には、金属探知機ゲートを通り、金属類の持ち込みは一切禁止されています。また、超強力磁石モップで細かい金属物の混入も防いでいます。
X線検査
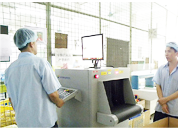
パッケージ終了後に検針作業を行います。ボールチェーンなど、検針機が通せない商品は、X線検査を行い全品目視で確認をします。(検針5回目)
カートン詰め
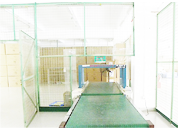
検針が終了した商品は最終のカートン梱包へ。カートンへ梱包後もカートンごとにもう一度検針機へ通します。(検針6回目)
出荷
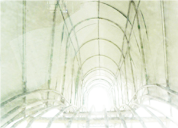
カートン詰めされた商品はこちらの滑り台を通って1階のコンテナへ運ばれ、日本へ向けて出発です。
検査体制について
- EN71
- RoHs
- 食品検査
- 重金属検査
- ST検査
各種検査のご依頼にも対応いたします。
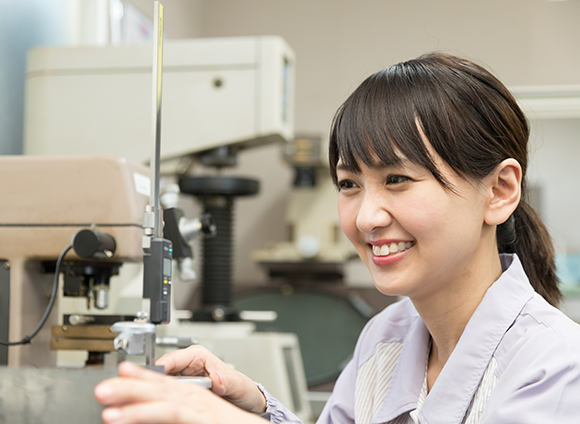